The History of Furukawa Co., Ltd.
Let us introduce the history of Furukawa Co., Ltd. which has been developed along with the history of Japan.
The History of Furukawa Co.,Ltd.
Meiji Era
The history of Furukawa Co., Ltd. dates back to 1875 when the founder, ichibee Furukawa began the copper mine operation, and since then, we have advanced with the modernization of Japan. From around 1900, our business began centering on the copper mine operation. We worked to innovate technologies with mining machines, such as imported rock drills, and owing to these technologies, the Ashio Copper Mine leaped ahead by producing the largest amount of copper in Japan. In the course of its development, a number of Furukawa Group companies were born.
During the Meiji Era, copper mine development became governmentally regulated and since the famous Ashio copper mine's pollution was rising in the area along the Watarase River in 1891, the copper mine operation faced a possible shutdown. We, however, applied the latest technologies available at that time and made every effort to preserve the best possible environment in order to solve the problem. In a manner of speaking, Ashio became the starting point for environmental measures implemented in Japan, and pollution prevention and by-product collection technologies developed in the process of solving the problem are invaluable assets that have been passed down to today.
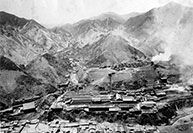
The Ashio Copper Mine is where the Furukawa Company Group began. At that time in Japan, industries had not yet fully developed so operation of copper mines was essential.
Taisho Era
The Taisho Era saw significant improvements in labor conditions of workers after the labor disputes that took place at the end of the Meiji Era.
At Furukawa Co., Ltd., applying the technologies cultivated through the maintenance of imported rock drills, we developed the first domestic hand-held rock drill (Ashio-type, No.3 rock drill). This was the start of our rock drill business. During the same period, we began developing pumps for slurry transportation at copper mines and coal pits.
Around this time, owing to the heavy industry expanded due to the First World War, a number of companies were established in Japan. In 1918, the predecessor of the current Furukawa Company Group, Furukawa Mining Co., Ltd. was established and the technologies and products developed at the Ashio Copper Mine were applied in a wide range of fields by Furukawa Mining Co., Ltd.
However, in 1920 - immediately after Furukawa became a company limited by shares, the depression attacked the Japanese economy. Our company, like all others during this period suffered and we were forced to close unprofitable mines.
(- 1918).
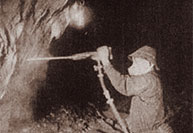
The first domestic rock drill was developed at Ashio. Because imported rock drills were too large and difficult to handle, development of a small rock drill that could accommodate the physique of Japanese operators had been expected.
Showa Era
In the midst of a tough economic situation including the Great Depression, Japan advanced towards the war between other countries. During the war, everyone in Japan had to cooperate in the war effort. In the government-controlled economy, the government controlled copper production and coal industries for the production of war supplies, and decided to increase production. To meet this demand, we reorganized the businesses and invested further into equipment and facilities by increasing capital.After the war, we developed further as the Japanese economy recovered. In the late 1950s, the demand for coal drastically dropped due to the energy revolution and the main energy source started shifting from coal to oil.
Consequently we withdrew from the coal business in 1970, and as import liberalization began, the volume of imported ores was increasing and copper veins were depleting leading us to close the Ashio Copper Mine in 1973. These events made us shift the focus of our Metals Segment from mining to smelting, as it now had to compete with overseas manufacturers.
At the same time, we began focusing on the growing fields of machinery and electronic materials. Possessing products such as rock drills and pumps developed by utilizing mining technologies accumulated over the years was a great advantage to us.
In 1987, the UNIC Corporation, a manufacturer of truck-mounted cranes, became a member of our group through M&A. Despite Japan's economic growth, infrastructure development was lagging so our products were appreciated and used in many infrastructure construction sites.
As well, our Research and Development Division was continuously researching effective uses of by-products generated during copper smelting process. High-purity metallic arsenic developed in 1962 is a material indispensable in the production of semiconductors and has grown to be the anchor product of the Electronic Materials Segment.
(-1945).
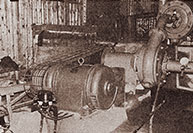
At the Oyama Works, pumps and mining machinery for copper mines were manufactured, not only for internal use but also to sell externally.
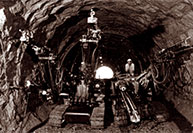
At the Takasaki Works, rock drills were massproduced and we established the position of a leading rock drill manufacturer.
(- 1961).
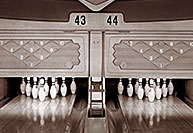
A huge bowling boom took place in Japan at that time. We manufactured bowling facilities and provided healthy entertainment.
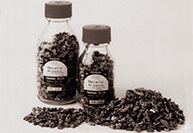
Arsenic is one of the by-products generated during the smelting stage of copper concentrates. It started getting attention as a semiconductor material around this time.
(- 1970).
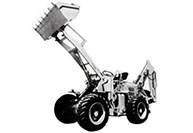
A large volume of our wheel loaders were exported as well and helped spread our name around the world.
(- 1991).
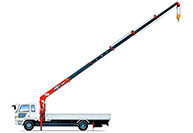
"UNIC" has become a synonym for truck-mounted cranes in Japan. UNIC Corporation (then Kyoei Kaihatsu Co., Ltd.) entered the Group and the name was changed to Furukawa UNIC Corporation two years later.
Heisei Era
In 1989, we changed the company name from Furukawa Mining Co., Ltd. to Furukawa Co., Ltd. and made a fresh start. In 1990 when the burst of the bubble devastated the Japanese economy, economic circumstances surrounding companies dramatically changed. Under this severe condition, companies further improved technological capabilities and promoted global business development in order to survive. We restructured the organization through the selection and concentration of the businesses and accelerated global expansion of the Machinery Segment. We launched rock drill sales companies and UNIC machinery manufacturers overseas one after another. In regards to materials, we enhanced and improved facilities for high-purity metallic arsenic.
We also enhanced our research system, for example, by integrating the development divisions of metals, electronics and chemicals in order to develop new materials through the unification of technologies.
In 2005, we spun off businesses and adopted a Group management system, and began as the Furukawa Company Group. This made it possible for us to make decisions more quickly and based on the characteristics of each business, to conduct agile management. Through this endeavor, we are making efforts to maximize the corporate value of the whole Group.
In 2015, we established the Furukawa Company Group's Management Philosophy and Action Guidelines, as well as the Furukawa Company Group's Vision for 2025, which marks the 150th year anniversary (in fiscal 2025) of the company's founding. All of this was undertaken in anticipation of the changes we expect to see in the business environment.
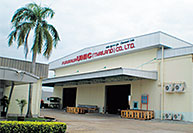
This is an affiliate company for the UNIC business established in Rayong, Thailand, which manufactures truck-mounted cranes and other products.
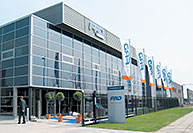
This is an affiliate company for the construction and mining machinery business established in Utrect, Holland, which distributes rock drills and other products.
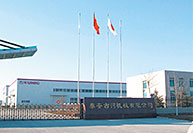
This is an affiliate company for the UNIC business established in Taian, Shandong, China, which manufactures and distributes truckmounted cranes and other products.
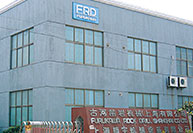
This is an affiliate company which deals with the construction and mining machinery business established in Shanghai, China and distributes rock drills and other products.
Reiwa Era
In 2020, the unprecedented global pandemic of COVID-19 had a major impact on Japan. Here in Japan, we saw occurrences like declarations of states of emergency and requests issued urging people to refrain from going out.
As we see an increase in the pace of social changes, such as in terms of the COVID-19 pandemic and the advent of a decarbonized society, our response to various challenges will lead to the creation of new markets.
At the Furukawa Company Group, we have set forth as an important policy the improvement of the value of the Furukawa brand through marketing-based management which incorporates CSV perspectives toward fruition our Vision for 2025, which we established to facilitate the realization of our Management Philosophy. We will continue contributing to the creation of social value taking the form of social infrastructure development and the bringing to fruition of a safe and environmentally friendly society, while we will go about generating corporate value by providing infrastructure, products, technologies, services, and other elements serving to aid in the solving of social issues.
In 2021, we consolidated the head office functions of our group companies dispersed around the Tokyo area and moved our head office to Tokiwabashi Tower in Otemachi, Tokyo.
Technologies that evolved in diversified fields in response to the demands of the times
We have been applying technologies that we acquired from operating copper mines to diversified fields in response to the demands of the times. Such technologies and products are continuously evolving with the changing times.
It is no exaggeration to say that the main support for the current Furukawa Company Group comes from the foresight of pioneers who introduced the latest equipment in the Meiji era, as well as the inquiring minds of the engineers who, not content with conventional technologies, worked on the development of new technologies and products.
It has been more than 140 years since our founding. If we look back at the history of the products that we manufacture and sell today, we can see a unique story of technologies handed down through the years.
Low-cost and low-pollution technologies - Revolutionary flash smelting
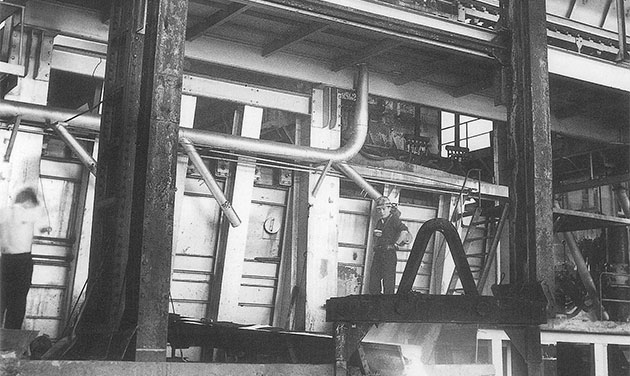
Smelting technology is used to separate metallic copper from copper concentrates and is required for the operation of copper mines. "The blast furnace smelting method" which combusts coke in the furnace and smelts copper ores became common from the late 1800s onwards.
We, on the other hand, developed a revolutionary smelting method by making unique modifications to the technology imported from Outokumpu in Finland. This technology called "Furukawa/Outokumpu flash smelting technology" smelts copper using thermal energy generated when sulphur and iron in copper concentrates react with oxygen and therefore enabled fuel-free smelting, which significantly reduced costs.
In addition, it makes possible the sophisticated collection of sulphur dioxide which causes environmental pollution, which enabled efficient sulphuric acid manufacturing. The first plant which applied this technology started operation in 1962. This flash smelting is highly-acclaimed as one of the top-level smelting technologies in the world and has been adopted in a number of smelting facilities in Japan and abroad.
"Anzen Senichi": Beginning of Safety Campaigns
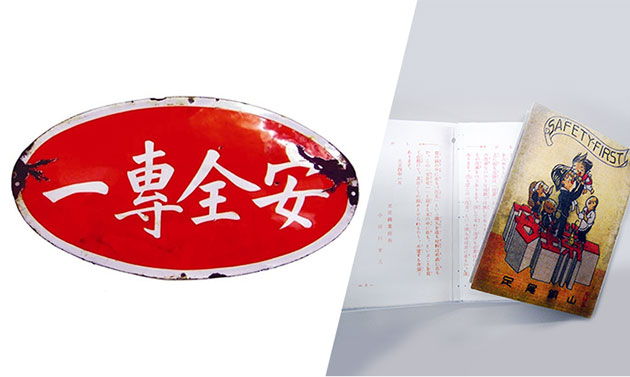
The Ashio Copper Mine, which built the foundation of the development of our group, was the birthplace of pollution-control technology and the industrial safety movement in Japan. In 1912, after a visit to the United States to study copper mining and smelting technology, Masayuki Odagawa, the manager of the Furukawa Kogyo Ashio Mining Office (now, the Furukawa Co., Ltd. Ashio Office), brought back the concept of "Safety First" that was advocated by an American steel company and translated it as "Anzen Senichi". After that, "Safety First" (translated as "Anzen Senichi") signs were displayed inside and outside mine shafts and safety awareness took root in the minds of employees thanks to elements like the creation and distribution of safety-related reading materials (directions for operation) and the subsequent promotion of safety-related activities at the Ashio Copper Mine. This is said to be the beginning of safety movement in Japanese industry. The forerunner of "Anzen Daiichi" ("Safety First") signs now displayed at construction sites and factories was the "Anzen Senichi" ("Safety First") sign. That message has been firmly inherited by the Japanese industrial safety movement.
Slurry transportation technology used in mines made highly-functional and durable pumps
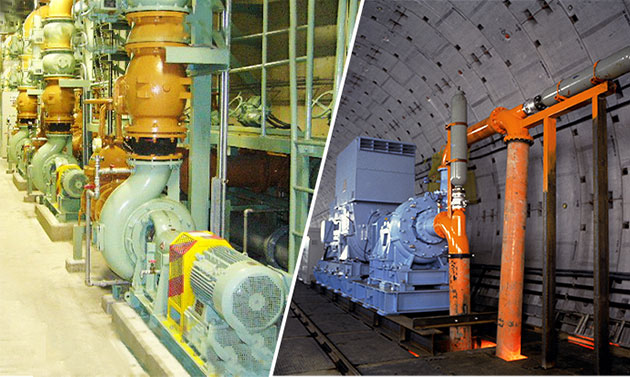
At mines, including copper and coal mines, work performance and efficiency greatly depend on slurry transportation capacity. We began manufacturing pumps for use by our company in the early 1900s in order to transfer slurry (water mixed with solids such as stones, mud and metals) from the dressing plant to the treatment plant outside the premises at the Ashio Copper Mine and started selling them on the general market after the war.
The greatest feature of our pumps is that they are highly durable and can transport slurry smoothly even in severe water conditions, utilizing the know-how that we accumulated at copper mines. We are now developing and manufacturing pumps for various applications in order to meet diversified requests. Our pumps are used for wastewater discharge from places of business and plants and for sludge transportation at sewage treatment plants. In addition, they are used to transport soil at tunnel construction sites using shield tunnel machines, specifically, the Trans-Tokyo Bay Expressway (Aqualine) tunnel/bridge, underground tunnels on the Tsukuba Express and the tunnel under the Bosphorus Straits in Turkey. They have also become essential tools at various wastewater discharge infrastructures.
From hand-held rock drills to large drilling machines
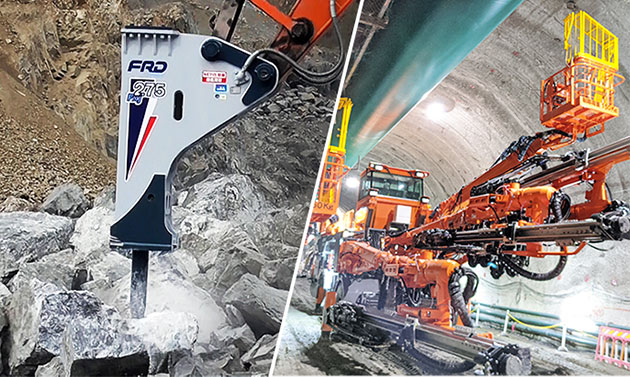
What is essential for the modernization of copper mines is improvement of drilling technologies. At the Ashio Copper Mine, when the company was first founded, workers dug by hand until imported rock drills were introduced in 1885. Then, a works was built in Ashio to repair imported machines and to manufacture replacement parts. In 1914, we successfully developed a domestic hand-held rock drill that could accommodate the physique of the Japanese operators. We started on the path to becoming a leading rock drill manufacturer.
In more recent years, we developed a Tunnel Drill Jumbo using rock drill technology to drill holes in mountains for setting blasting powder at tunnel construction sites. Our Tunnel Drill Jumbos have been used at the majority of tunnel construction sites in Japan such as the Hakkoda and Seikan tunnels on JR (formerly JNR) railway lines and the Kan-etsu tunnel on the Kan-etsu Expressway. Furthermore, our products to which this rock drill technology is applied, such as hydraulic crawler drills which make downward holes in rocks for blasting powder and hydraulic breakers which crush rocks, are utilized around the world in infrastructure construction and at open pit mining sites.
Continuously evolving UNIC products to respond to the demands of the times
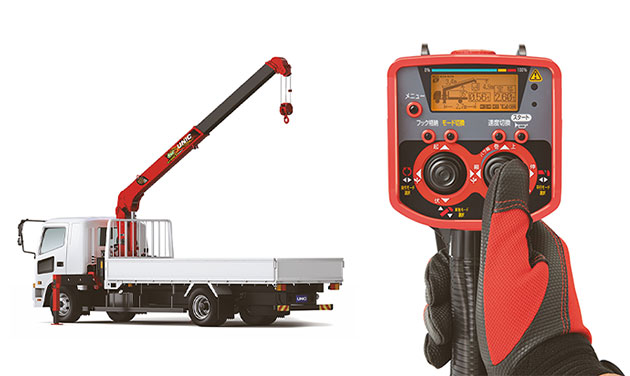
UNIC cranes, synonymous with truck-mounted cranes, were invented in 1961 during the post-war reconstruction period. Having hanging, loading, transport on a single truck significantly improved work efficiency. We have always developed UNIC products in order to meet the demands of the times, such as improving lifting capability and adopting long booms to expand work areas as well as labor saving with radio and remote controls.
The fuel-efficient and low-noise U-can ECO series (medium to large truck-mounted cranes) was released in 2006. Thanks to the development of the ECO pump system", the series achieved the same performance level with approximately 50% less engine speed compared to our conventional products. It also won the ECCJ Chairman's Prize* at the 18th Energy Conservation Grand Prize event organized by the Ministry of Economy, Trade and Industry, for the first time in the industry, for these significant carbon dioxide emission and cost reduction effects. UNIC has continuously evolved and will continue to evolve in the future.
By-products generated through the smelting process are transformed into valuable resources
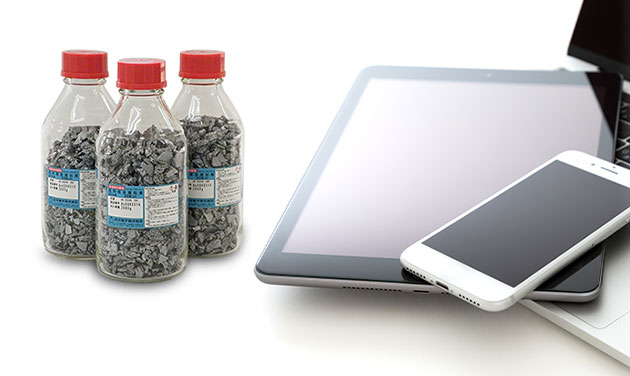
When copper ore is smelted, by-products such as concentrated sulphuric acid and rare metals are generated. We used to consider such by-products without worth but, as science advanced, it was revealed that they were valuable resources with many uses. We saw a strong potential for arsenic, one of the by-products, and developed Japan's only arsenious acid manufacturing technology in the early 1900s. At that time arsenic was used in glass and pesticides, etc., but it soon started gathering attention as a material for semiconductors. We began developing high-purity metallic arsenic in 1961 and we are now capable of producing metallic arsenic with a purity of 99.999995% and have the largest share both in the Japanese and global markets. High-purity metallic arsenic is used to make gallium arsenide semiconductors which are indispensable for electronic devices in smartphone and tablet etc. In this way, our high-purity metallic arsenic is contributing to the advancement of the information society.